Composite Fiber Co-extrusion (CFC) is an additive manufacturing process for production of lightweight and strong composite parts with a complex shapes and internal structures. The process is based on embedding continuous composite fiber into the fused plastic through the use of a specially developed print head. The print head shown in the figure below includes two extruders which are plastic (FFF) and composite (CFC). The composite extruder has two inlets and one nozzle. The central inlet is for composite fiber and the lateral inlet is for plastic. The CF goes through the central channel and is coated by molten plastics supplied through the lateral channel into the heat block of the extruder. The CF with the molten plastic is laying up layer by layer through the extruder nozzle on the work surface. Thus, a composite part reinforced with continuous fibers is forming. The plastic extruder has one inlet for plastic
filament and one nozzle.
The technology allows manufacturing high-quality reinforced materials while using the flexibility of shapes and a wide range of plastics.
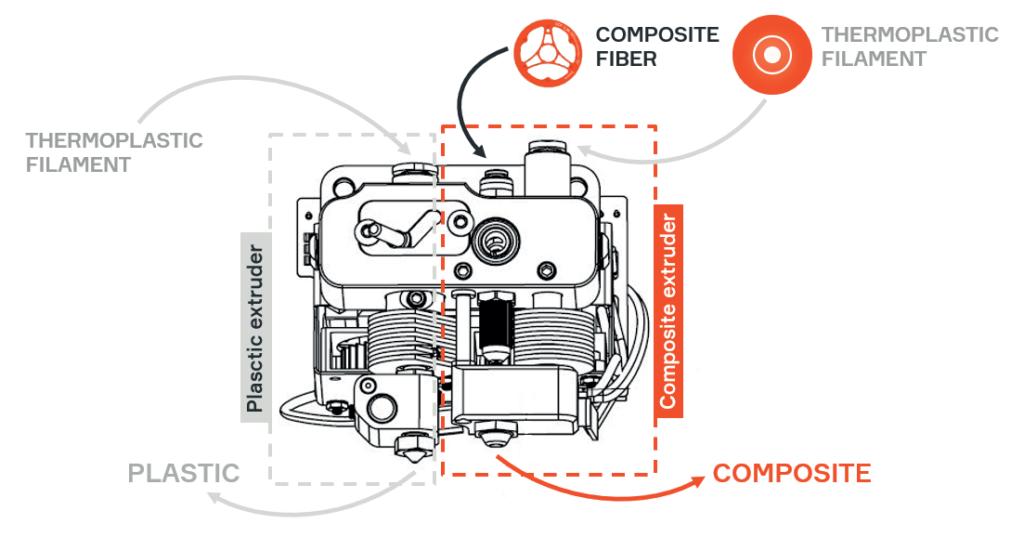
The technology allows to use various plastics with processing temperatures up to 270°C. You can use ABS, PLA, PETG, PA, and PC plastics. The material can be varied to achieve the best operational or economic parameters of the parts depending on the goals.