1.Disclaimer
This User Manual is the main document for Composer CFC printers, it is provided with the delivery package. The Manual guides correct operation, maintenance, and troubleshooting of Composer CFC printers manufactured by Anisoprint.
Please follow this User Manual when operating and maintaining the equipment. Failure to follow the guidelines may lead to poor quality of printed parts, damage to the printer, or cause injury, please read the User Manual carefully.
2.Safety instructions
2.1.Electromagnetic compatibility
Composer CFC printers were tested for compliance with 2014/30/EU guidelines. According to compatibility tests, the printer is a class A device, which means it can cause additional electromagnetic interference when used at home.
2.2.General Precautions
Carefully study all precautions before using the printer. When in operation the user should follow all operation precautions for electrical equipment.
An explanatory note to graphic symbols:WARNING – indicates a potentially dangerous situation that may result in serious injury or fatal outcome.
CAUTION – indicates a potentially dangerous situation that may result in minor or moderate injury.
NOTE – indicates a situation that may result in equipment failure.
Basic precautions:
WARNING: do not plug the printer in without grounding!
WARNING: do not touch the print head when printing. The nozzle temperature may be up to 270°С!
WARNING: do not try to repair the printer yourself!
CAUTION: do not use the printer in facilities with ambient temperature lower than 15°C or higher than 35°C!
CAUTION: avoid penetration of water in electronic components of the printer to prevent short-circuit.
CAUTION: disconnect the power cord in case of modifications and maintenance.
CAUTION: when connecting power cord to the power line, be sure that the printer ON/OFF switch is in <O> position.
CAUTION: use the printer in ventilated locations.
CAUTION: the printer is a source of noise; do not use it in leisure areas.
NOTE: do not turn on the printer if the print head is disconnected!
NOTE: place the printer on a level and rigid surface in order to ensure convenient and easy operation with all elements.
NOTE: when in operations, do not place any objects inside the working zone and inside the printer; do not cover the printer and the air vents.
NOTE: if the printer is under warranty maintenance, it is not recommended to perform any repair independently!
NOTE: before the first operation be sure that all packaging materials are removed.
NOTE: do not use the printer without the glass at the buildplate!
2.3.Precautions when working with carbon fiber
CFC 3D printing implies work with carbon fiber. Please bear in mind that carbon fiber is a good electrical conductor. The flow of current through carbon fiber leads to its instant ignition, which may result in injuries and equipment failure.
WARNING: do not place the printer next to uncovered sockets and laboratory power supply sources in order to avoid ignition of carbon fiber. Carbon fiber is a good electrical conductor.
If for some reason there occurred a breakage of the composite fiber, do not touch the place of the direct fracture with unprotected skin. Carbon fiber consists of thousands of thin and sharp threads that can easily get stuck in the skin, even intact fiber can sometimes cause splinters.
In case of fiber breaking small suspended particles may accidentally get into the eyes or respiratory system. If it is necessary to examine the components of the Composer CFC Printer at a close distance, where carbon fiber is outside the protecting tube, be sure to wear safety glasses and protecting mask.
WARNING: do not work with carbon fiber without personal protective equipment – gloves, safety glasses, and mask.
2.4.Warning symbols
For safety reasons the following symbols can be found on the printer case.
Parts marked with this symbol heat up to high temperature and may cause skin burns
Places of grounding connections
Areas of nono-protected contacts under voltage of 220-240V. WARNING: do not take off the protective cover marked with this symbol
NOTE: please read this manual before using the printer. Keep this manual during the whole period of operation of the equipment
CAUTION: the manufacturer reserves the right to introduce minor changes (not affecting safety requirements and operation characteristics) in the design of the printer! Some design changes may not be covered by this user manual
2.5.Compliance statement
The product is certified in accordance with the applicable technical regulations. The service life is 2 years from the date of purchase provided the product is not used for anything other than the intended purpose according to the rules and recommendations described
in this User Manual.

Product certificate: №181299324
Certificate is valid: from 09.11.2018 through 08.11.2021
Product and services certification authority: Technický skúšobný ústav Piešťany, š.p.
This equipment complies with Directive WEEE 2012/19/EU for disposal of electric and electronic equipment and devices. This equipment must be disposed of in accordance with the applicable local waste and safety regulations. To ensure safety when disposing the equipment it is necessary to follow generally accepted practices for safe operation when disposing of equipment and devices.
3.Composite Fiber Co-extrusion
Composite Fiber Co-extrusion (CFC) is an additive manufacturing process for production of lightweight and strong composite parts with a complex shapes and internal structures. The process is based on embedding continuous composite fiber into the fused plastic through the use of a specially developed print head. The print head shown in the figure below includes two extruders which are plastic (FFF) and composite (CFC). The composite extruder has two inlets and one nozzle. The central inlet is for composite fiber and the lateral inlet is for plastic. The CF goes through the central channel and is coated by molten plastics supplied through the lateral channel into the heat block of the extruder. The CF with the molten plastic is laying up layer by layer through the extruder nozzle on the work surface. Thus, a composite part reinforced with continuous fibers is forming. The plastic extruder has one inlet for plastic
filament and one nozzle.
The technology allows manufacturing high-quality reinforced materials while using the flexibility of shapes and a wide range of plastics.
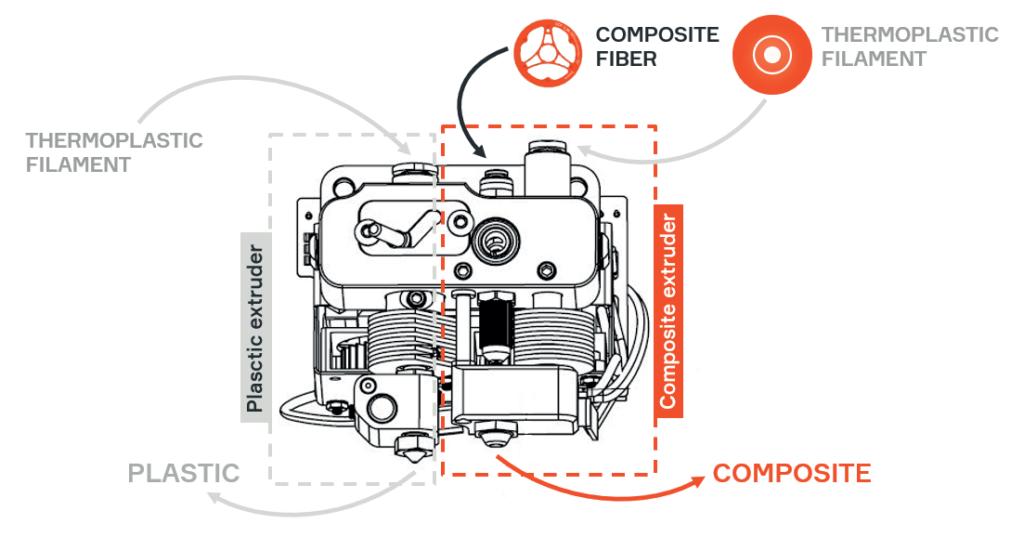
The technology allows to use various plastics with processing temperatures up to 270°C. You can use ABS, PLA, PETG, PA, and PC plastics. The material can be varied to achieve the best operational or economic parameters of the parts depending on the goals.
4.Overview
Composer is a desktop CFC 3D printer available in two formats: A4 and A3. Both machines have heated buildplates and closed chambers.
5.Basic specifications
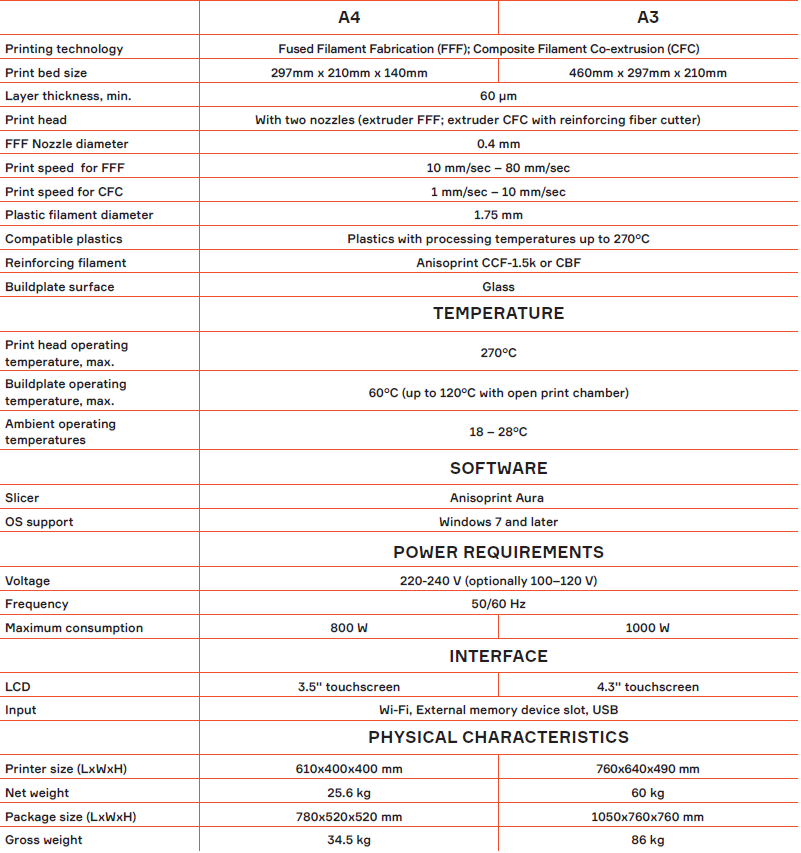
6.Delivery package
Items in the package:
- Composer CFC printer – 1 pc.
- Plastic filament spool – 2 pc.
- Anisoprint CCF-1.5k fiber spool – 1 pc.
- Tool kit – 1 pc.
- Personal protective equipment kit – 1 pc.
- Spare parts kit – 1 pc.
- Memory card SD – 1 pc.
- User Manual
7.Composer operations
7.1.Main screen
After switching on the Composer printer, you will see the main screen, which brief description is given below.
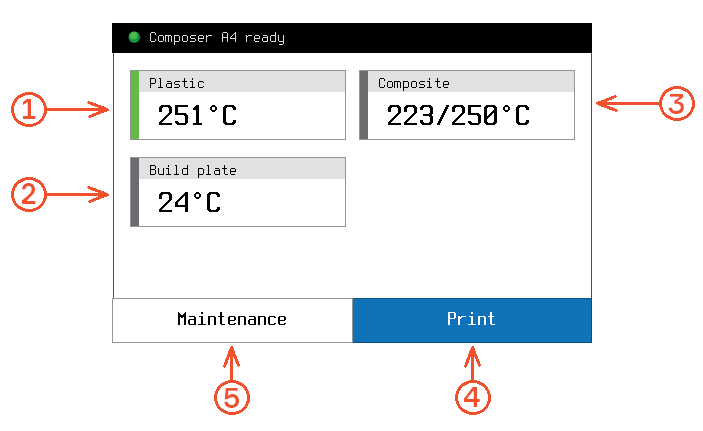
1 – Plastic extruder temperature settings button
2 – Buildplate temperature settings button
3 – Composite extruder temperature settings button
4 – print button. To start the print, press this button and select the file of your part from memory device
5 – Maintenance options button. Here, the following options are available:
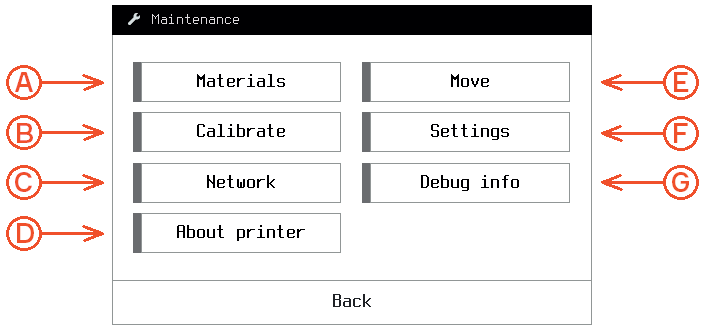
A – Loading/unloading plastic filaments and composite fiber
B – Calibration of the buildplate / Z-axis / print head (Z offset)
C – Printer connection settings
D – Key information about the printer (serial number, version info, build date)
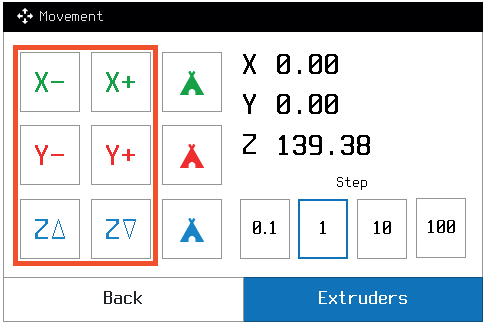
Use axes movement control buttons to move by axes
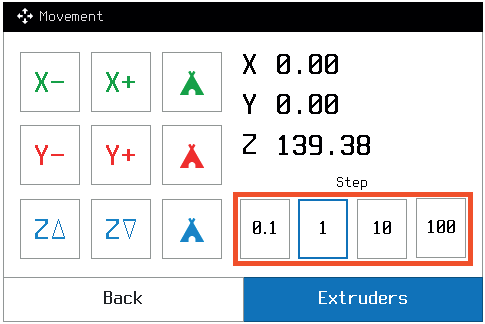
Select movement increment
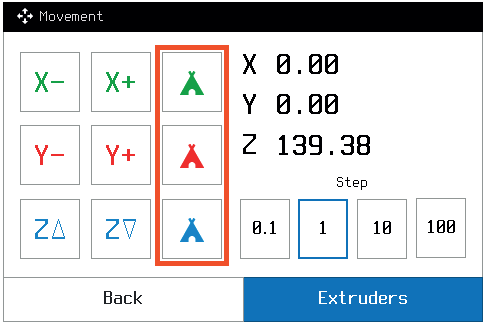
Use home positioning buttons for tool homing
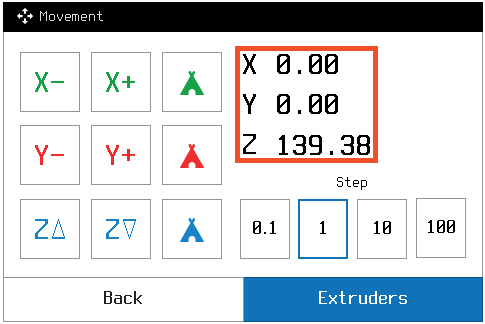
Control XY coordinates of extruder and Z coordinate of
buildplate
Also, you can control material supply. To do it press Extruders button. Here, the following options are available:
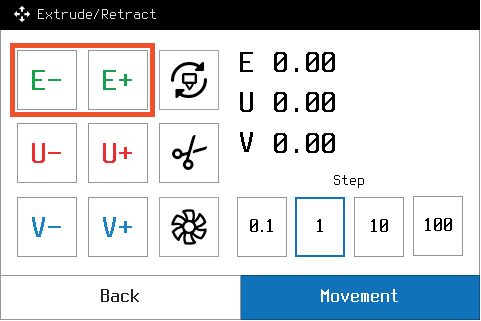
Retract/supply plastic filament in plastic extruder
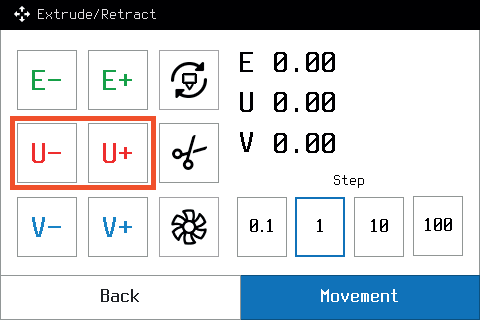
Retract/supply composite fiber in composite extruder
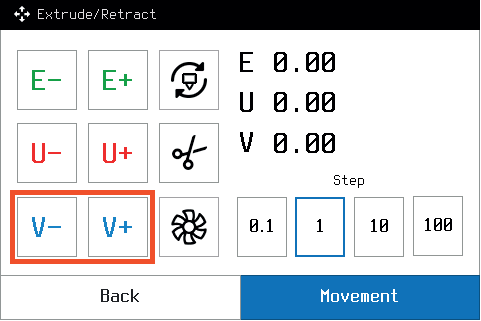
Retract/supply plastic filament in composite extruder
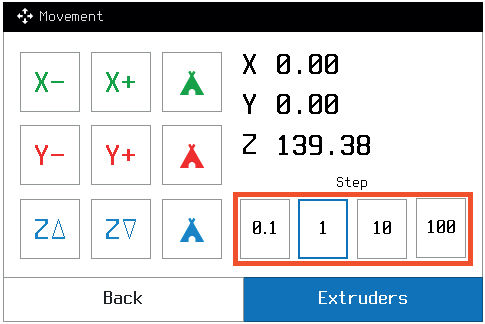
Select increment for material retract/supply
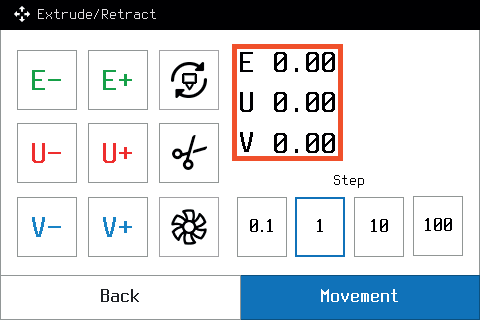
Control material feed coordinates
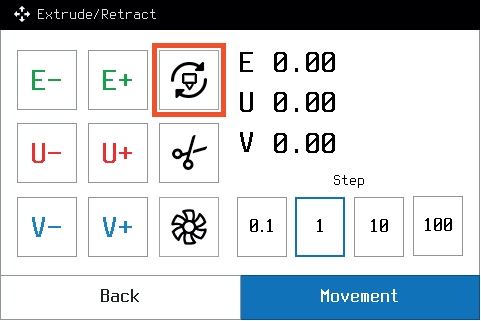
Change active extruder
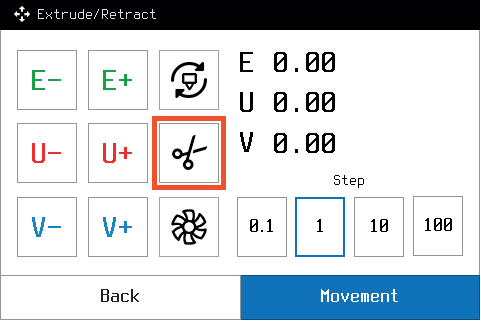
Initiate fiber cutting mechanism
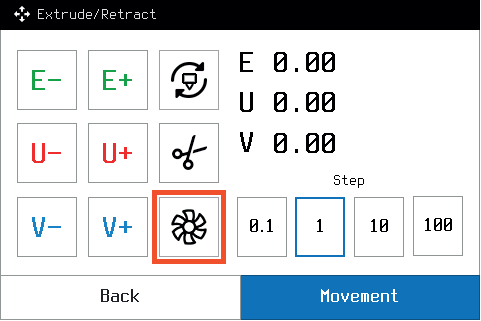
Switch on/off nozzle blowing fan
E – Composer axes positioning button. Here, the following options are available:
NOTE: these parameters directly affect the printer functionality!
F – Printer settings button.
G – Debug info (service information)
7.2.Installation
Your Composer requires several assembly steps before you can start printing.
Unpack the printer and place it on a reliable flat surface, protected from strong vibrations. Adjust the printer feet to compensate for any unevenness of the surface if needed.
1. Remove blue transportation tape to release the doors and print head
2. Unpack the glass print surface, place it on the buildplate and fix with the clamping clips
3. Using a hex key from the Tool kit, attach the spool holders to the back mount of the printer
4. Install the wipe station part on the station bracket on the right for A4 and on the left for A3 Composers. The size and color may vary with the printer model
5. Plug in the power cable
6. Calibrate the buildplate with an in-built procedure: at the home screen of the printer, go to Maintenance > Calibarate > Buildplate
7. Calibrate the Z-axis with a built-in procedure in Maintenance > Calibrate > Z-axis
7.3.Loading materials
1. Take the 3 spools (plastic, composite plastic, and fiber) out of package and place them
onto the holders.
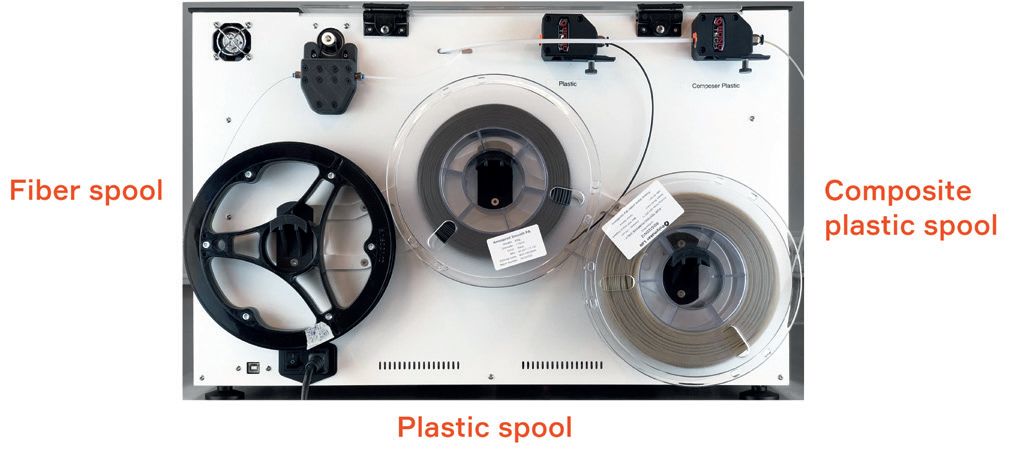
2. On the Composer screen, click Maintenance > Materials > and choose the material you want to load. Follow instructions on the screen.
NOTICE: Plastic can leak out of the composite heat block inlet during plastic filament loading in the composite extruder. Just remove the leaked plastic with tweezers to prevent dripping of the plastic on the printed part.
7.4.Buildplate calibration
Your Composer had already been pre-calibrated before shipping, but due to transport vibrations, it could be uncalibrated. Thus, you may need to go through the entire calibration procedure after the printer installation.
NOTICE: Clean and preheat the nozzles and the buildplate to its printing temperatures before all the calibration procedures (buildplate, Z axis, Z-offset) to prevent incorrect calibration.
You need to go through the buildplate calibration procedure after any changes affecting the positioning of the buildplate, e.g. shaking or moving the printer. While printing a large part occupying the whole buildplate area, you can notice layer thickness varies from one end of the part to another, which as well means the buildplate requires recalibration.
To start the calibration, go to the main screen, press Maintenance >Calibrate > Buildplate. Follow the instructions. First, you will be asked to set the plastic nozzle in approximately 1 mm from the buildplate. The first of 3 points is to be set through the calibration menu,
the left and right corners are tuned manually by adjusting the regulation screws. Second, the procedure is to be repeated for fine-tuning, this time using a sheet of 80gsm paper to set the lowest possible gap between the nozzle and the buildplate. The paper must be sliding in the gap with slight friction.
It is recommended to calibrate the Z-axis right after the buildplate calibration.
7.5.Z-axis calibration
The distance between the buildplate and the plastic nozzle tip is quite an important parameter affecting the quality of your prints. You need to go through this procedure every time you replace the plastic nozzle or if you faced some issues with laying out the first layer of the print.
Press Maintenance > Calibrate > Z axis and follow the instructions. You will be asked to use a sheet of 80gsm paper to fine-tune the gap between the nozzle tip and the buildplate.
Print any file to verify the results of the calibration, paying attention to the brim and the first layer layup. You can tune the first layer height during the print, see IN-SITU TUNING OF PRINTING SETTINGS p7.9.
It is recommended to calibrate the Z offset right after the Z-axis calibration.
7.6.Z offset calibration
Z offset defines the relative position of the composite nozzle with respect to the plastic nozzle about Z-axis.
If the composite nozzle tip scratches the buildplate or previous layers, or the quality of vertical walls of your model is insufficient due to improper plastic layup, go through this procedure. Also, it is recommended to go through this procedure every time you replace the composite or/and the plastic nozzle.
On the screen of the printer, press Maintenance > Calibrate > Printhead > Comp. Z offset. and go through the built-in calibration procedure by following the instructions on the screen.
7.7.XY offset calibration
X and Y offsets are the physical distances between the tips of the plastic and the composite nozzles at the Composer print head, shown in the picture below.
You need to go through XY offsets calibration once after composite or/and plastic nozzle replacement. In order to calibrate XY offsets, print the special service code NozzleOffsetTest.gcode from the external memory device supplied with your Composer printer. You can also download it from support.anisoprint.com
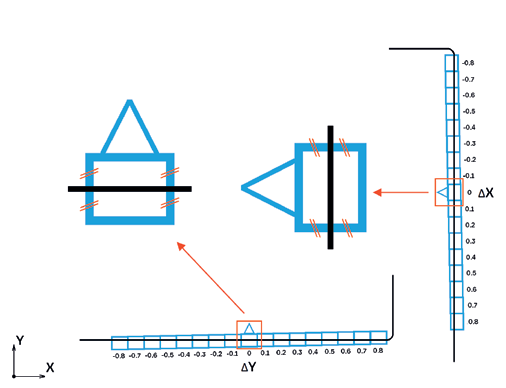
If the XY offsets are well-calibrated, the composite fiber is in the middle of the central cells, like it is shown in the scheme
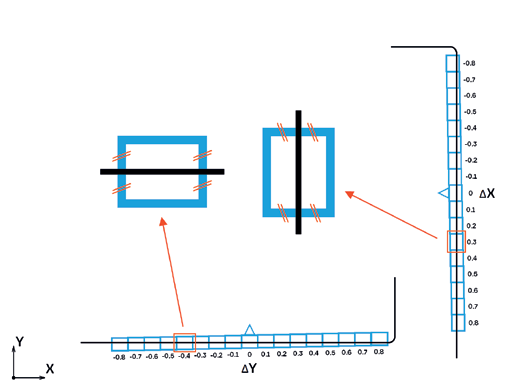
If the composite fiber deviates from the middle position of the central cells, like it is shown in the reference scheme, you need to change your XY offsets values (i.e calibrate it)
In order to calibrate XY offsets, for every axis find the cell where the composite fiber is right in the middle as shown on the reference scheme (right picture). XY adjustment value for each axis is written near the corresponding cell. For the given example it is +0.3 for X offset and -0.4 for Y offset, which means that you need to add +0.3 to the original X offset and -0.4 to the original Y offset.
To change these values, go to Maintenance > Settings.
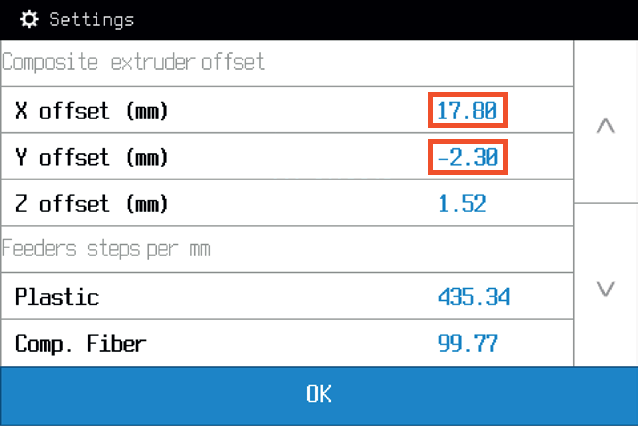
The new offsets will be
17.80 + 0.30 = 18.10 for X offset,
and -2.30 – 0.40 = -2.70 for Y offset.
After adjusting the offsets, reprint the offset test and make sure that composite fiber is in the middle position for both X and Y central cells.
7.8.Test print
The test part “Wall bracket” introduces you the capabilities of Composer and also serves as a combined quality test. You can find the “Wall bracket” for the particular profile in the Aura Welcome window.
- Use recommended adhesive for your plastic filament, e.g. Magigoo Original for transparent PETG or Magigoo PA for polyamide (PA).
- After the print start, both extruders, plastic and composite, start to heat. When the composite extruder reaches the extrusion temperature, the composite nozzle will print a short purge line (composite thread) on the build plate. It must be glued to the surface and look smooth and uniform.
- After printing the purge line, the machine will start the first plastic layer. Check that the plastic perimeters look the same along the part. The first layer must be nicely glued to the build plate.
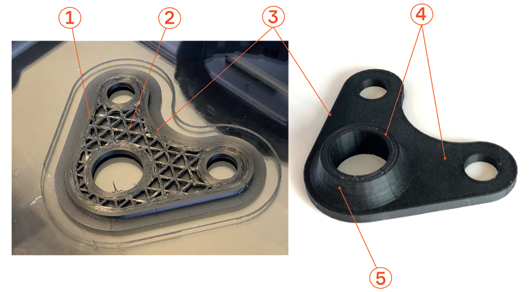
1 – Fiber perimeters
2 – Cellular fiber infill
3 – Outer plastic perimeters
4 – Plastic top cover
5 – Plastic shell
- After several plastic layers, the machine will start the first fiber perimeter and fiber cellular infill. Due to the process features, it may look a bit wobbly, but the layup visual quality will normalize later on. If the fiber goes off trajectory or doesn’t glue to the previous layer, go through the Z OFFSET CALIBRATION procedure p 7.6.
- During the next plastic-composite cycles, fiber perimeters will be surrounded by plastic ones. Make sure the plastic and fiber perimeters do not intersect and fiber perimeters are laid without displacements.
- Inspect the printed part paying special attention to side walls quality. Check the surface smoothness visually and compare it to the photo above. In case of poor side walls quality, go through the Z OFFSET CALIBRATION procedure p 7.6.
Congratulations on your first print!
7.9.In-situ tuning of printing settings
Some basic operations with the printer are still available during the printing.
After you start the print, the PRINTING screen appears. Here you can pause your print by pressing the PAUSE button, or adjust the printing process by pressing the CONTROL button.
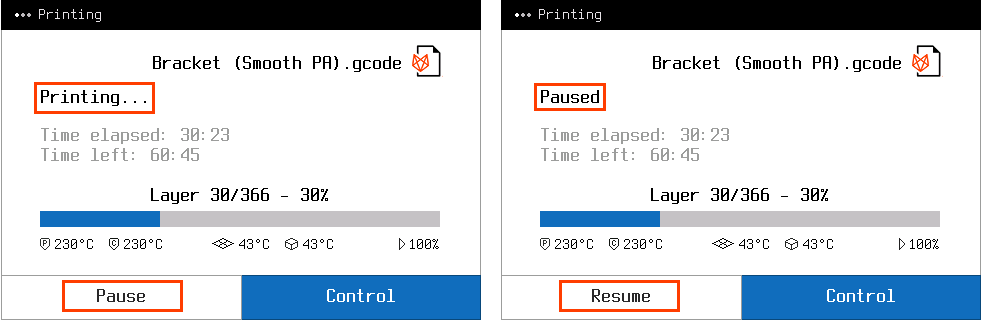
After the print is paused, the print head and buildplate will return to their default positions. Extruders stay hot during the pause. You can see all the control capabilities over the paused print in the picture below.
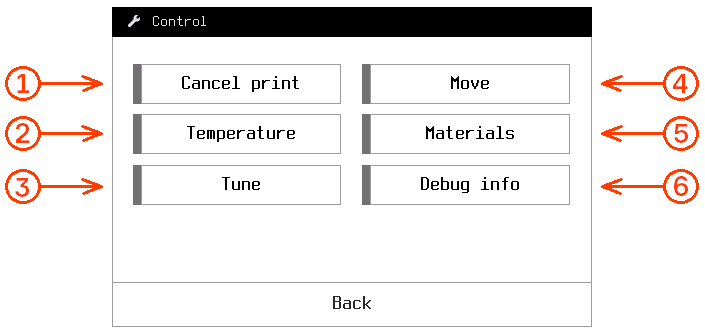
Here, the following settings are available:
1 — Cancel the print
2 — Cool or heat up extruders and buildplate
3 — Printing parameters tuning. Here, the following settings are available:
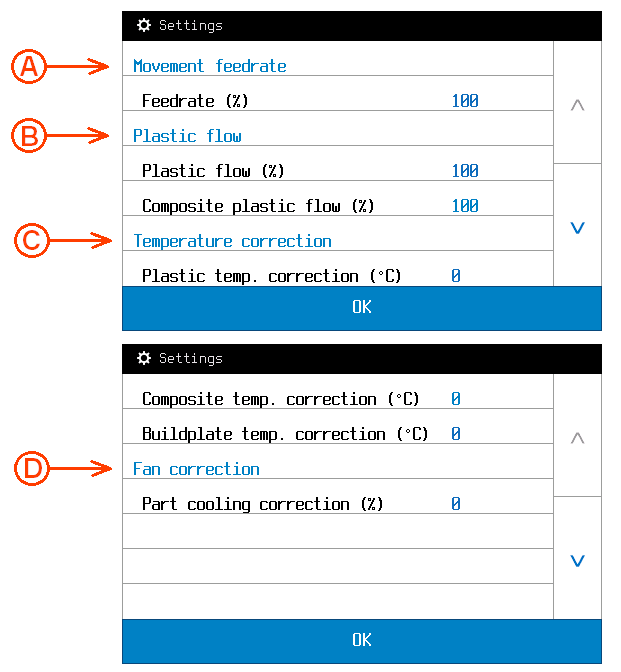
A – Movement feed rate determines printing speed (100% by default, can be varied within a range of 25 to 200%).
B – Plastic flow parameters adjust extrusion coefficients of plastic in a percentage manner. Plastic flow range is from 25 to 150%).
C – Temperature correction value increases or decreases predefined temperature on set increment (0 °C by default, can be varied within a range of -100 to 100 °C). Note that the temperature is limited by 270 °C for extruders and 120 °C for buildplate.
D – Fan correction value increases or decreases predefined fan power (0 % by default, can be varied within a range of -100 to 100%).4 – Axis positioning (see MAIN SCREEN p 7.1)
5 – Loading/unloading materials (see LOADING MATERIALS p 7.3)
6 – Debug info is service information (for service engineer if required)
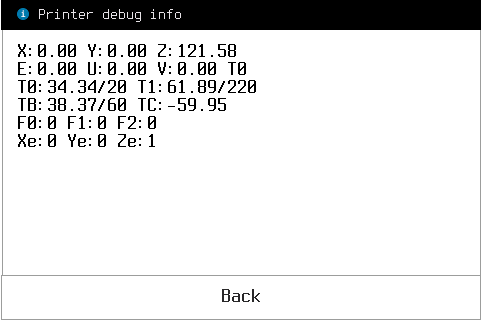
Press the RESUME button to continue the print from the stopping point.
Press the CONTROL button in printing mode to tune the printing process. The screen when the CONTROL button is pressed in the printing mode is shown below.
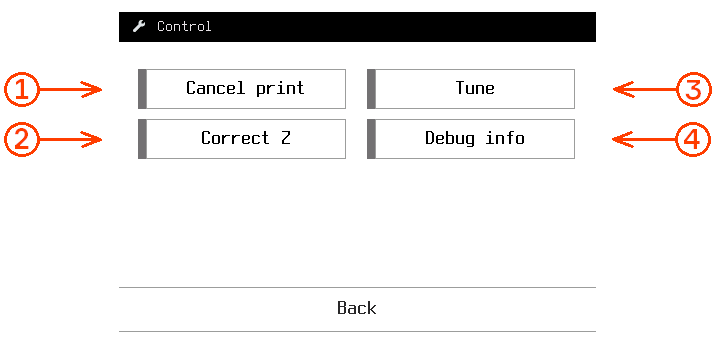
Here, the following settings are available:
1, 3 and 4 buttons are the same as for paused print
2 – Correct Z. If the first layer of the print is too thick or thin you can move the buildplate up or down by 0.01/0.1/1 mm to achieve the optimum thickness of the first layer. Notice, that this setting does not influence the Z axis calibration.
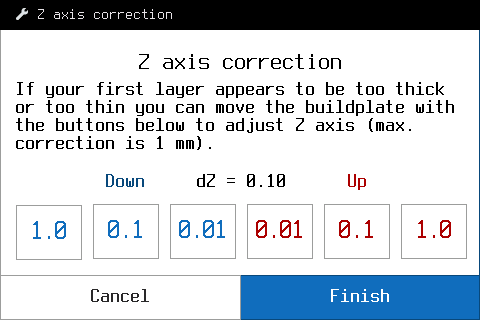
7.10.WI-FI connection
In order to find out whether your printer supports Wi-Fi, you need to check the version of the printer (see MAIN SCREEN). If the version contains “nw” letters – your printer supports Wi-Fi.
To connect your printer to Wi-Fi follow the instructions below.
- Update your Composer firmware to version 1.2.0 or later. You can download the firmware from Anisoprint Support Portal. On the \Guide page you can find instructions for firmware update.
- Check the version of network bridge software (see MAIN SCREEN p 7.1).
- If the NW ver. is n/a please turn the printer off and on and wait for one minute (the network bridge booting process takes about a minute after power on).
- If the NW ver. is 0.1, please follow additional instructions marked with an asterisk. Also, please update the Network software to the latest version.
- To update the network bridge software to the latest version, see NETWORK BRIDGE SOFTWARE UPDATING p 7.11.
- Go back to Menu from About Printer screen.
- Go to Network -> Connections.
- For NW v0.1: please wait for 10 seconds before pressing the «Choose Wi-Fi network» button. If the list of networks is empty, please go back and try again.
- Press Choose Wi-Fi network.
- For NW v0.1: if the desired network is not on the first page, please wait for 10 seconds before going to the next page by pressing the arrow on the right side of the screen.
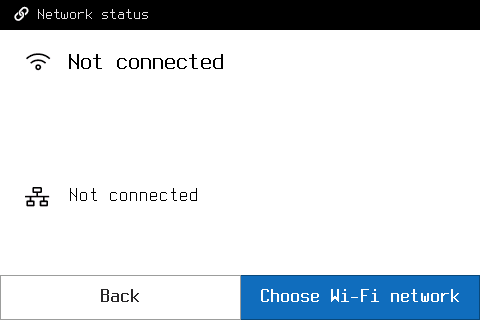
7. Select your Wi-Fi network from a list. If the network is secured, enter the network security key and press OK.
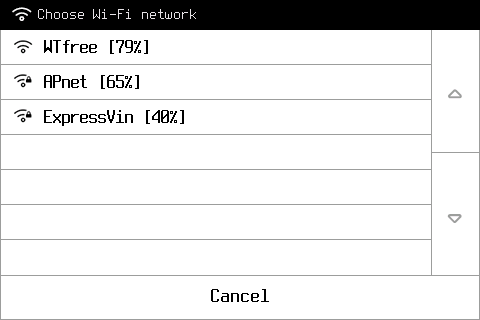
7.11.Network bridge software updating
To update the network bridge software please connect your Composer to the Internet through Wi-Fi. The updates are performed automatically 4 times a day if a new version is available.
Note:
- The updates are performed from Ubuntu Snap Store, if your printer is behind a firewall,
please check the following document to make sure that these network addresses are available for the machine: https://forum.snapcraft.io/t/network-requirements/5147. - If your network can’t have access to the Internet, please contact Support
(support@anisoprint.com) to receive instructions for an offline update.
8.Maintenance
Timely maintenance of the printer ensures correct printer operation and consistent print quality. The recommended schedule for maintenance operations is given in the table below:
8.1.Plastic nozzle replacement
You might need to clean the inner surface of a nozzle – chemically or mechanically, for that, you need to remove the nozzle and install it again. Here are the steps.
- Using the 2mm hex key from the tool kit, loosen the side screws of the fan bracket. Remove the fan bracket carefully, it should hang on wires.
- Heat the plastic extruder to the printing temperature (270 °C for Smooth PA).
- Using the 7 mm socket wrench, unscrew the plastic nozzle from the plastic extruder, do not use too much force to avoid damaging the nozzle.
- Clean the nozzle or use a new one.
- The nozzle is installed with a special copper washer to avoid leakages of plastic from the extruder. Be sure to remove it from the old nozzle and install on the threaded end of the new one.
CAUTION: all extruder part can be hot!
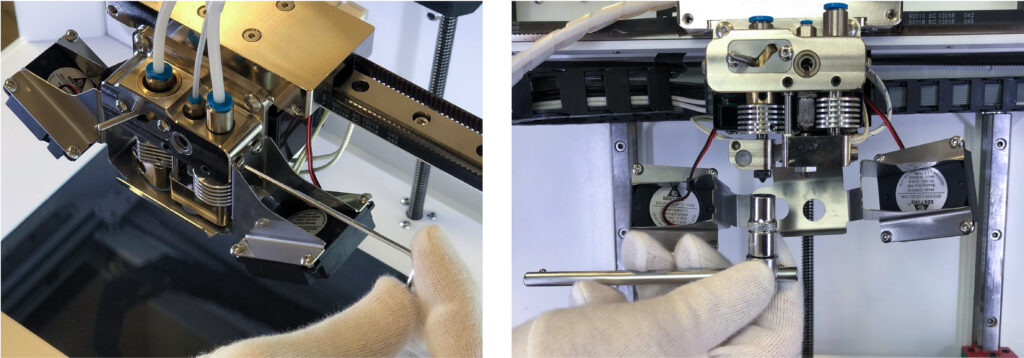
8.2.Plastic nozzle cleaning
You might need to clean the plastic nozzle, for instance – if the under-extrusion occurs. Follow the next steps to clean the plastic nozzle:
- Heat the plastic extruder to the printing temperature (270 °C for Smooth PA).
- Clean the nozzle with a cleaning needle from the tool kit. To clean the contact surface of the nozzle, use the brass brush from the tool kit.
3. To finish the cleaning, feed about 50mm of plastic to the extruder.
8.3.Composite extruder channel cleaning
To prevent fiber clogging the extruder cleaning is recommended before each print. This will ensure the successful printing of the parts without fiber clogging.
CAUTION: all extruder parts can be hot!
- Heat composite extruder up to composite plastic printing temperature (or a bit higher). On the main screen press Composite extruder temperature button and set required temperature.
2. Clean the contact surface of the composite nozzle by brass brush from the set of cleaning tools.
3. Insert the barbed needle from the set of cleaning tools into the composite nozzle. Spinning the needle, push it through the extruder, until the end of the needle is in the inlet hole of the extruder. Be careful not to break the needle. Pull the needle down and clean it by tweezers so the barbs are clean.
4. Remove material, pushed out of the inlet of the extruder with tweezers.
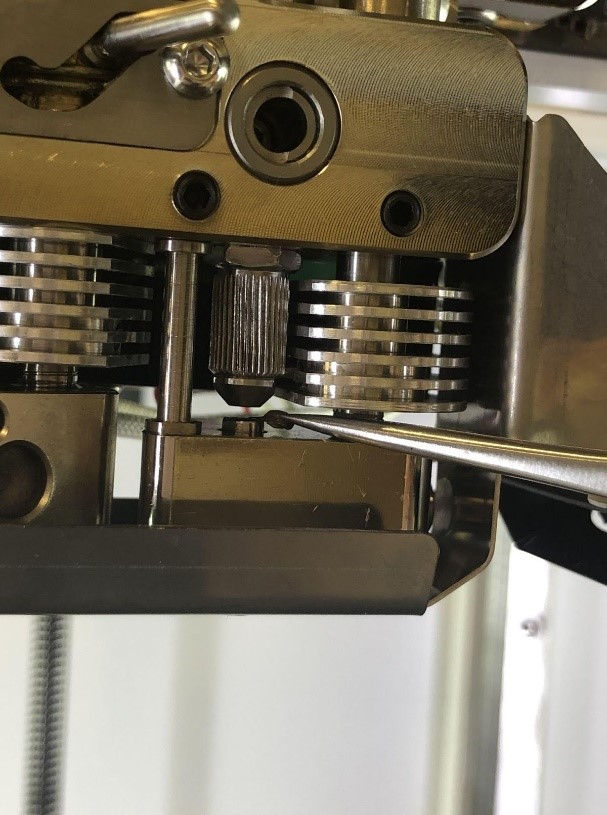
5. Repeat points 3. – 4. until the needle is clean and the remains of the material stop pushing out of the inlet of the extruder.
6. From the main screen go to Maintenance > Move > Extruders, change Step to 10 mm and feed 50 mm of the composite plastic filament (press V+ button 5 times). You should see clean plastic exiting from the nozzle and inlet.
8.4.Lubrication
To extend the service life of a Composer, mechanical parts of the product must be serviced on a regular basis. For this purpose, you need to lubricate the moving parts: guides of X, Y, Z axes, Z-axis screw, and the nozzle switch mechanism. The delivery package includes special lubricants for all of these parts. Lubrication of mechanical parts of the printer is recommended at least once every six months.
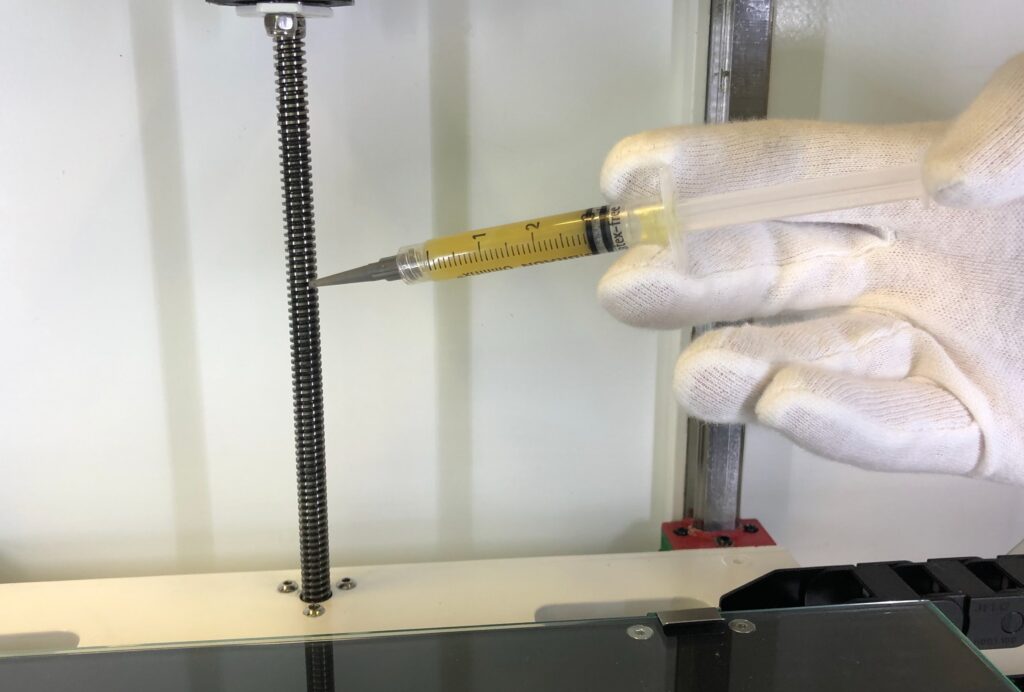
8.5.Keeping the printer clean
If you use the printer frequently, small particles of plastic and fiber may accumulate in the internal space. From time to time clean the printer platform from accumulated particles and dust with a microfiber and a vacuum cleaner.
The glass of the buildplate will inevitably accumulate particles of plastic and fiber, fixing varnish or glue. To improve the adhesion of the part during printing and the quality of the first layers of the product, it is recommended to clean the surface of the glass before each print with a damp cloth.
9.Printing materials
9.1.Plastics
There are two different plastics, included in the Delivery Package: Smooth PA and CFC PA. These plastics are developed to be used in couple for the best performance. Although you can use these plastics in a combination with other types of plastic in EXT and OPEN packs.
Smooth is branded thermoplastic polymer material based on polyamide PA12 filled with chopped carbon fibers and developed by Polymaker especially for use with Anisoprint Composer 4/3. The material is intended for 3D printing of secondary (unreinforced) zones of composite parts reinforced with continuous fibers and facing surfaces. The material is supplied as filaments with cross-sectional diameter of 1.75 mm. Smooth features low moisture absorption and makes use of anti-warping technology. Perfect surface quality and ease of use also make it the best choice for most users.
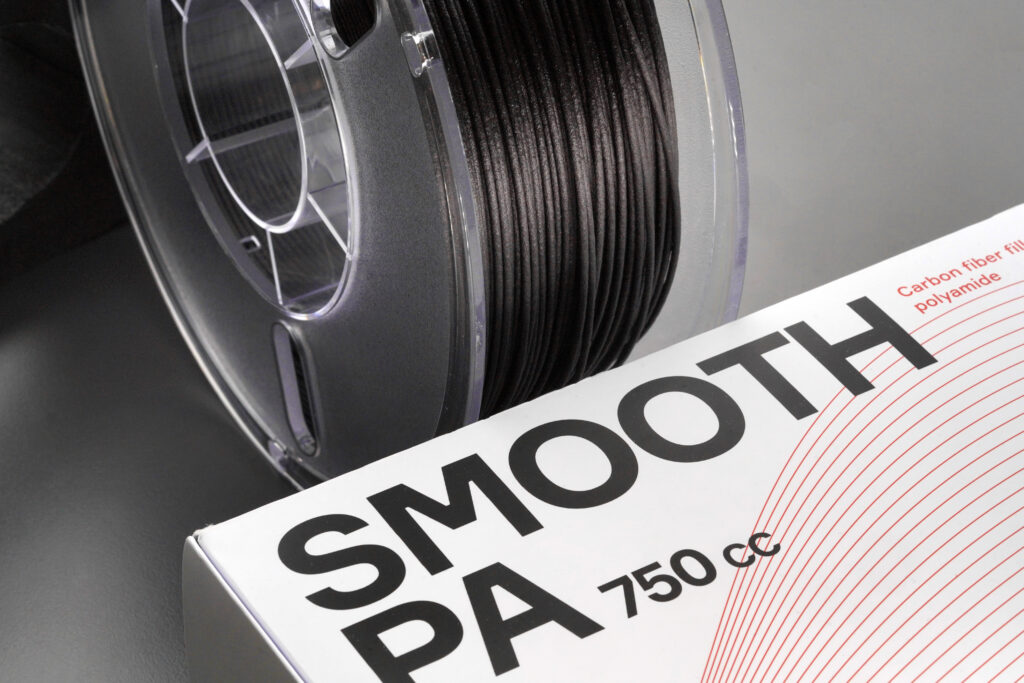
CFC PA is thermoplastic polymer material based on polyamide PA12 and developed by Polymaker especially for Anisoprint CFC (continuous fiber co-extrusion) process. CFC is applied as a matrix material in 3D printed composite parts reinforced with continuous fibers. The material is supplied as filaments with cross-sectional diameter of 1.75 mm.
CFC PA has a relatively low viscosity that allows good binding of fiber layers. This plastic is also low absorption grade and can be printed from open-air for a decent amount of time.
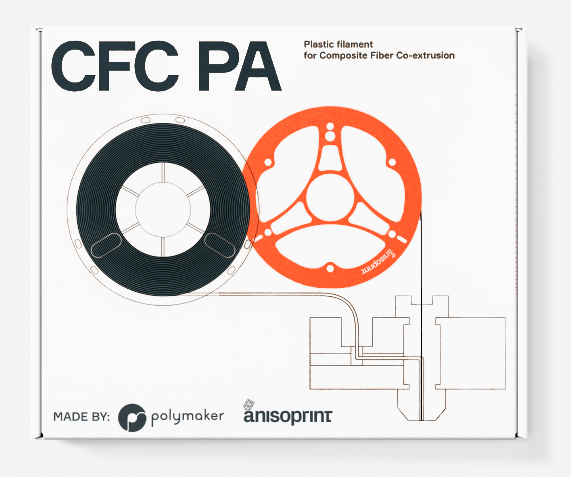
CAUTION: supply Smooth PA to the plastic extruder, CFC PA to the composite extruder
If you use the EXT pack, in addition to Smooth PA and CFC PA profiles you will be able to use plastics from the following polymer families: PLA, PETG, PC, PA, ABS. There are material profiles in Aura available for them that are thoroughly tested and provide stable excellent results.
OPEN material database package includes all materials from NEAT and EXT packages and contains elaborated profiles for any plastic with a melting point below 270°C.
9.2.Reinforcing fiber
A specially prepared patented composite fiber Anisoprint CCF is used for printing with reinforcement. It provides a high-quality adhesion to plastic. Anisoprint CCF is a composite reinforcing fiber in the form of a tow made of thousands of ultrathin carbon monofilaments, impregnated with a special polymer composition ensuring high-quality impregnation and adhesion between the polymers and the fiber. Composite fiber is used to reinforce the plastic during the manufacturing of the part.
NOTICE: do not print with composite extruder without composite fiber. Otherwise, plastic leakage from the inlet hole may occur.
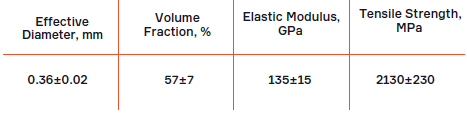
CAUTION: the manufacturer dislaims any responsibility for the effects of use of non-recommended materials, improperty stored materials; when other materials instead of recommended reinforcing fiber are user. Use of materials non tecommended in this manual may result in damage or complete failure of the equipment
9.3.Storage of materials
Most plastics used in 3D printing tend to accumulate moisture (hygroscopic). In its turn, the presence of moisture in filament will cause boiling of the liquid during printing, which will result in an uneven supply of plastic and as a consequence in a defect in the quality of the final part. Some types of plastics are less sensitive to presence of moisture in the surrounding space, but for a better surface quality it is recommended to store plastic filaments in places with a minimum amount of moisture. The solution of this problem is to use a dryer before printing.
Carbon fiber, which is part of the composite bundle, accumulates less moisture than plastics, but it is also a hygroscopic material. Similar to plastics it is required to choose spaces with minimum moisture content in the air for its long-term storage.
NOTICE: do not use heater dryers for Anisoprint CCF (Composite Carbon Fiber) and CBF (Composite Basalt Fiber). Being heated above 40°C for a long time (more than several minutes), carbon and basalt fibers become brittle and improper for printing.
10.Software
Anisoprint Aura is a slicer that prepares 3D models for manufacturing parts with Composer CFC printers. It allows you to print both full plastic and composite parts by using plastic and composite extruders respectively.
Aura prepares the 3D model, generates reinforcing fiber trajectories in each layer, and allows to adjust reinforcement scheme to create strong and lightweight parts. It allows combining micro and macro layers, making it possible to print an infill with thick layers and an external shell with thin layers. This feature results in a shorter printing time without loss of quality.
Aura is easy to use, has a stylish interface and a wide range of practical and versatile features. Aura can generate reliable supports for printing complex objects and shows the printing model layer by layer. The model processing is fully automated and performed on your PC (not in a cloud), ensuring confidentiality and safety of your data.
You can download Aura from the website anisoprint.com/aura/
10.1.Interface
After installation, described on the website, you can open Aura and the main window will appear. You can see the description of the main menu on the picture below.
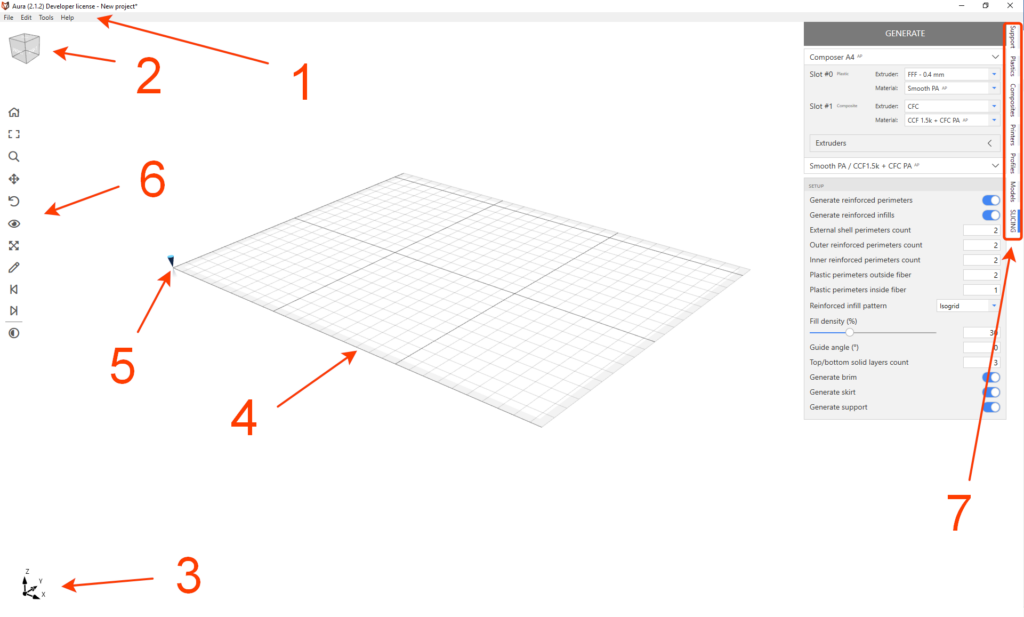
- Main menu
- View cube
- View axes
- Buildplate
- Origin of the coordinate system
- View toolbar (zoom, pan, rotate, etc.)
- Main tabs
10.2.Slicing the model
To prepare your model for printing, you should go through the following steps:
- In the main menu go to “File” and click on the “Open model…”.
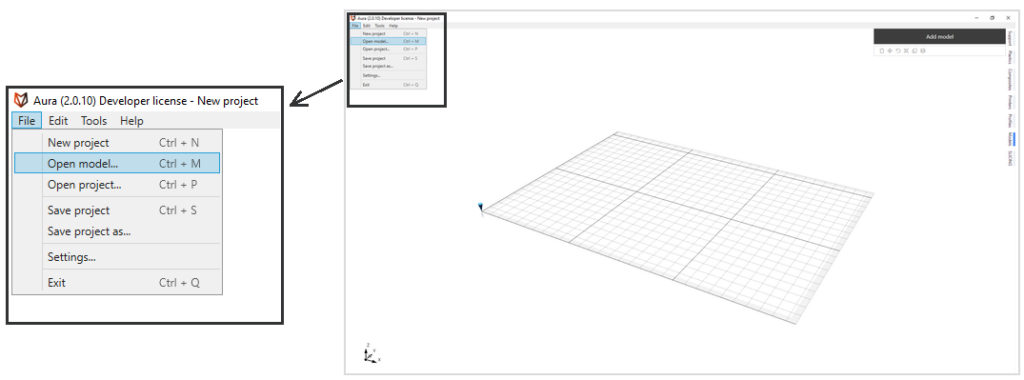
2. Choose your model file and place the model on the buldplate. Note, that your model should be in one of the following formats: *.stl, *.step, *.stp, *.3ds, *.obj.
3. Adjust printing settings in the SLICING panel from the main tabs and click GENERATE.
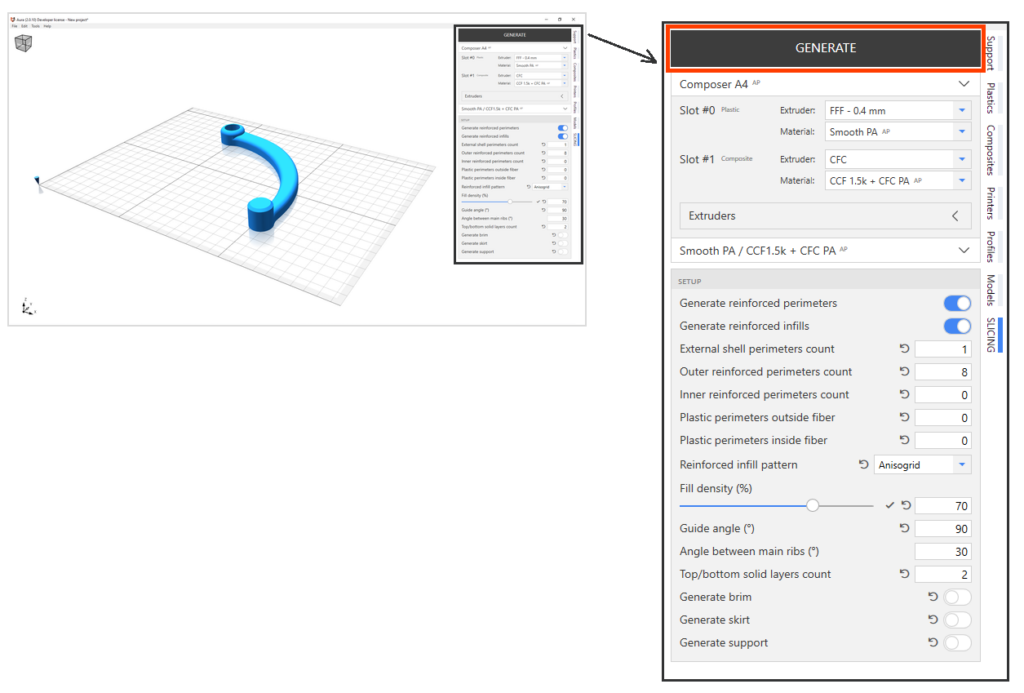
4. After a successful generation of the code, you will be offered to view the code or save it to a file. You can press VIEW CODE to see the layout of your model in a 2D or 3D view.
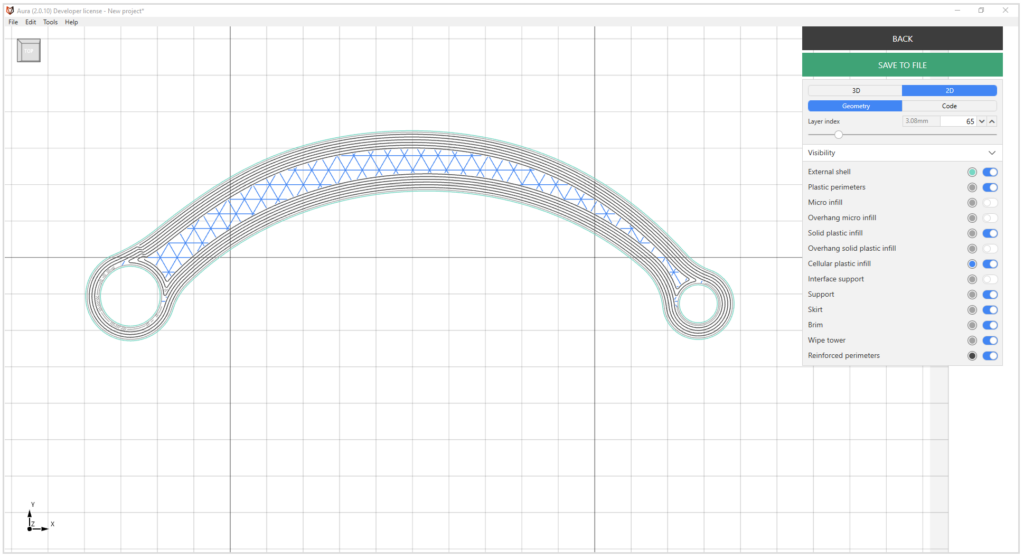
5. You can save the code by pressing the SAVE TO FILE button. If you want to change printing settings you need to press the BACK button, change desired parameters and press the GENERATE button again.
You can find more detailed Aura overview and video tutorials on the website anisoprint.com/aura/
10.3.System requirements
The recommended system configuration is the following:
- DirectX 10 compatible graphics card, e.g. ATI Radeon 3000 series, Nvidia GTX 300 series
- Display resolution 1920 x 1080
- Intel Core i3 or AMD Athlon 64
- 400 MB hard disk space
- 8 GB RA
11.Troubleshooting
There are several issues that you may face in case of improper operating Composer 3D printers. If an issue occurs, try to find it in the present Manual section and address it yourself.
11.1.The part get unglued from the buildplate during printing
- Check whether the temperature of the buildplate matches the recommended buildplate temperature for the plastic.
- An insufficient amount of varnish/glue is applied to the buildplate surface. Increase the amount of adhesive.
- If points 1. and 2. are met but the issue still exists, then the height of the first layer is incorrect. Go through the Z AXIS CALIBRATION procedure, p. 7.5
11.2.Plastic is not extruded from the nozzle
- Check whether the plastic is correctly loaded in the feeder; whether plastic filament comes to the print head.
- Check that the temperature of the extruder meets the recommended processing temperature of the plastic.
- If points 1. and 2. are met, then the nozzle is clogged. Go through the PLASTIC NOZZLE CLEANING procedure, p. 8.2; or PLASTIC NOZZLE REPLACEMENT procedure, p. 8.1.
11.3.Fiber is not extruded from the nozzle
- Check whether the fiber is correctly loaded in the feeder. Whether the fiber comes to the print head.
- Check whether the temperature of the composite extruder corresponds to the temperature of the plastic processing for the fiber.
- If points 1. and 2. are met, then the fiber is clogged. See FIBER IS CLOGGED INSIDE THE COMPOSITE EXTRUDER, p. 11,6.
11.4.Strings and poor surface quality of printed part
There are some issues that may cause poor quality of the final part, including plastic under-extrusion, plastic stringing etc.
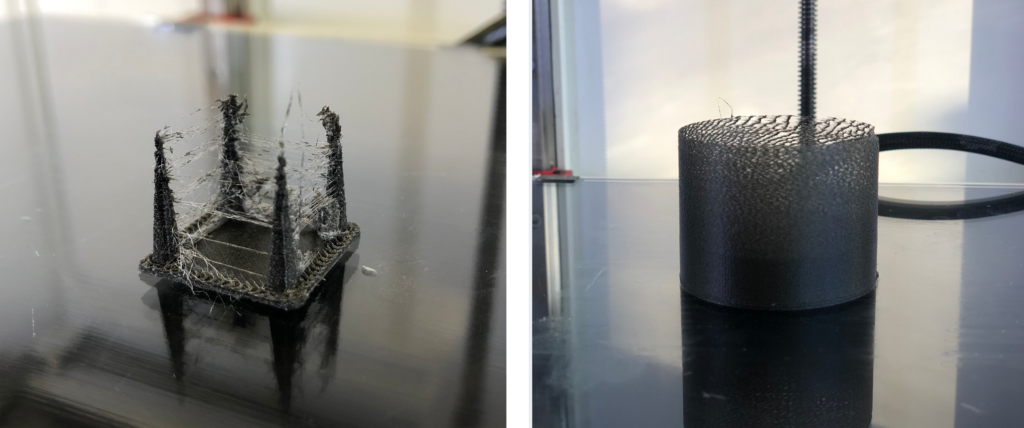
- Check whether the plastic was dried before printing. Most plastics tend to absorb moisture that affects the quality of the printed part. Dry plastics in accordance with the material specification if required.
- Check the nozzle surface cleanliness. Clean the nozzle by brass brush from the tool kit if required (see PLASTIC NOZZLE CLEANING, p. 8.2).
- If points 1. and 2. are met, then the nozzle is worn out. Long-term operation of the nozzle may cause wear that manifests in strips, gallings, or roughness of the inner surface of the nozzle, so you may need to replace the nozzle. Go through the PLASTIC NOZZLE REPLACEMENT procedure, p. 8.1 if required.
11.5.Plastic leaks out of the composite heat block inlet
There are several issues that may cause plastic leakage. If such an issue occurs, heat the composite extruder and remove plastic, leaked out of the heat block inlet with tweezers. Before this procedure, cancel the active print if there is one.
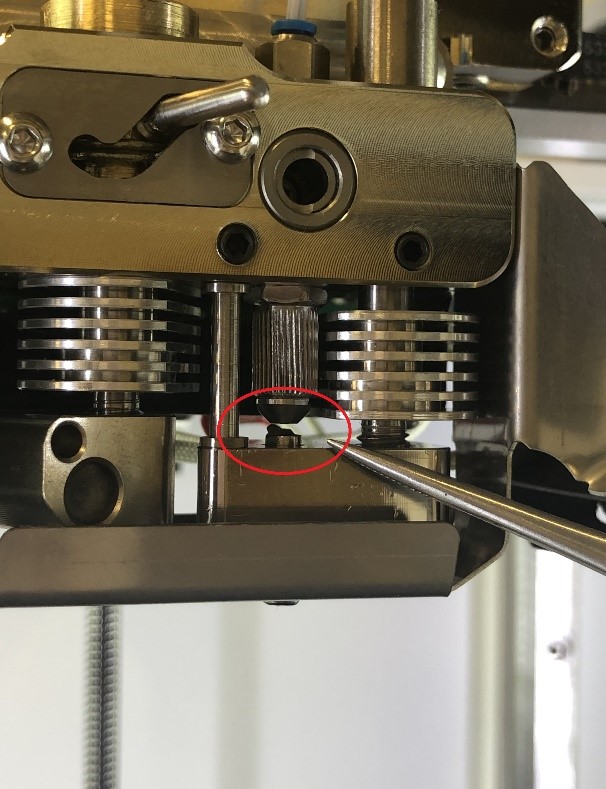
After the leaked out plastic is removed, go through the issue identification procedure described below:
- Check Z axis calibration. Incorrect Z axis calibration may cause plastic leakage on the inlet of the composite heat block. Go through Z AXIS CALIBRATION procedure, p. 7.5.
- Check Z offset calibration. Low Z offset value may cause accumulation of composite plastic inside the heat block and further leakage from the inlet. Go through Z OFFSET CALIBRATION procedure, p. 7.6.
- Check whether the composite plastic was dried before printing. The presence of moisture in filament will cause boiling of theliquid during printing, which will result in an uneven supply of composite plastic. Dry plastics in accordance with the material
specification if required.
NOTICE: lack of composite fiber in the heat block or stop of its feed can cause plastic leak of the composite heat block inlet. This can happen during the composite plastic loading or its manual feed. The plastic fills the heat block and goes out through both the nozzle and the inlet simultaneously.
11.6.Fiber is clogged inside the composite extruder
For some reasons (incorrect printing parameters or improper maintenance), composite fiber may stop feeding, i.e stop coming out of the heat block. It means that composite fiber is clogged inside the extruder. For this case, a cleaning procedure is described below.
- Heat composite extruder up to composite plastic printing temperature (or a bit higher). On the main screen, press the Composite extruder temperature button and set required temperature (see point 1. from COMPOSITE EXTRUDER CHANNEL CLEANING, p. 8.3).
- If there are some fibers, sticking out of the heat block, remove them, by pulling down with tweezers.
- Clean the contact surface of the composite nozzle by brass wire brush from the set of cleaning tools (see point 2. from COMPOSITE EXTRUDER CHANNEL CLEANING, p. 8.3).
- Insert the barbed needle from the set of cleaning tools into the composite nozzle. Spinning the needle, push it through the extruder, until the end of the needle is in the inlet hole of the extruder. Be careful not to break the needle. Pull the needle down
and clean it by tweezers so the barbs are clean. You may need to push/pull the needle with effort if the fiber is clogged tight, use pliers for this purpose. - Remove material, pushed out of the inlet of the extruder with tweezers.
- Repeat points 4. – 5. until the needle is clean and the remains of the material stop pushing out of the inlet hole of the extruder.
- From the main screen go to Maintenance > Move > Extruders, change Step to 10 mm and feed 50 mm of the composite plastic filament (press V+ button 5 times). You should see clean plastic, exiting from the nozzle and inlet.
11.7.Fiber is clogged inside the cutter
- Heat composite extruder up to composite plastic printing temperature (or a bit higher). On the main screen press the Composite extruder temperature button and set the required temperature (see point 1. from COMPOSITE EXTRUDER CHANNEL CLEANING, p. 8.3).
- Using the 2mm hex key from the Tool Kit loosen the side screws of the fan bracket. Remove the fan bracket carefully, the fan bracket stays hang on wires.
- Using the 2mm hex key from the Tool kit, loosen 2 set screws on the front of the extruder. Remove the composite extruder by pulling it down. Be careful, composite extruder stays hot so it can melt wires of the fan bracket.
- Using the wrench key or pliers unscrew the fiber guiding bushing.
- Check for the broken fibers inside the fiber guiding bushing.
5.1 If the fiber is clogged inside the fiber guiding bushing, clean it with a needle from the set of cleaning tools, by pushing the fiber out of the bushing.
NOTICE: fiber guiding bushing consists of two parts. If you face any problems while cleaning the channel, you can disassemble it and clean the parts separately.
- Using tweezers from the Tool kit remove clogged fiber from the cutter.
- Assemble the extruder in reverse order.
11.8.Fiber is broken before the cutter in the PTFE guiding tube
This may happen if the cutter is positioned incorrectly, so the fiber could not pass through it and was broken in the PTFE guiding tube (see INCORRECT POSITION OF CUTTER, p. 11.9).
- Pull out the tube from the printing head, pressing the latch on both sides.
- Remove the excessed fibers from the tube.
- Connect the tube to the printing head.
11.9.Incorrect position of cutter
For the printer to operate properly, the cutter should be in a certain position. For some reasons (improper transportation, loose cutter bolt, etc.), the cutter may not be positioned correctly. To make sure the cutter is in the right position, go through the manual cutting procedure using Menu > Maintenance > Move > Extruders > “Scissors” button. If you cannot cut composite fiber, you should go through the cutter positioning procedure, described below.
CAUTION: while the printer is switched on, the servo is under voltage permanently, so if you try to tighten it with too much force it can lead to burning of the servo, please be careful and follow the instructions.
- Using the 2mm hex key from the Tool kit, loosen the bolt that fixes the cutter on the servo`s shaft.
- Using a screwdriver or tweezers from the Tool kit place the shaft by rotation so the slot is in vertical position (for the first type of the cutter, see left picture below)/align the grooves on the cutter and sleeve (for the second type of the cutter, see right picture below) and then slightly fix the bolt.
- Turn off the Composer and tighten the bolt. While tightening servo will rotate to its max angle and stop so you can tighten it.
- Turn on the Composer – servo will set on its “Zero angle”.
- Make sure that the top hole of the cutter sleeve is completely open and the cutter is firmly fixed. To check it, do the manual cutting procedure from the main menu or run NozzleOffsetTest.gcode from the external memory device supplied with your Composer printer. You can also download it from support.anisoprint.com.